For the long haul
Kitimat-Stikine, British Columbia. With more than 18,000 operating hours, underground mining’s largest battery-electric haul truck fleet is delivering marked productivity and environmental improvements for Newcrest’s Brucejack gold mine.
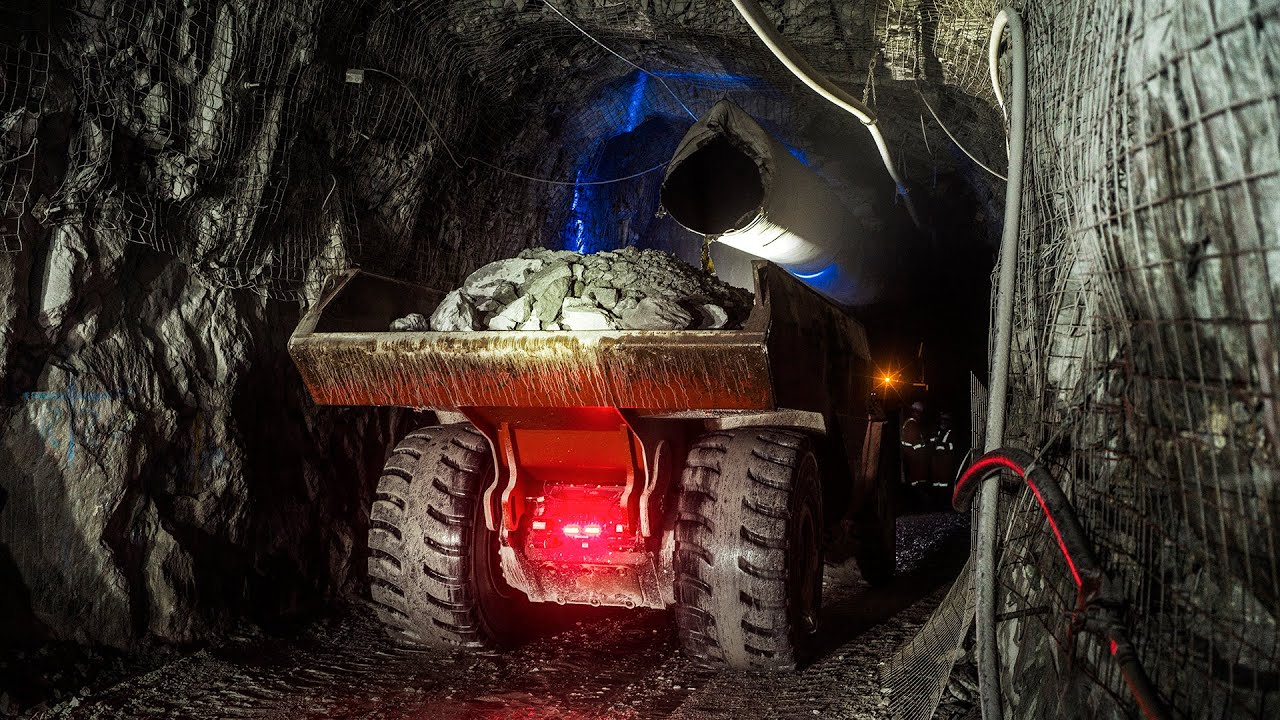
The final 11 kilometers of the access road to Brucejack mine, spanning a total distance of 76 kilometers from the nearest highway, passes through the Knipple Glacier. The glacier road – which all employees, contractors, equipment, parts, consumables and supplies must cross to reach the mine in the mountainous north-western British Columbia – requires year-round maintenance, from grading in summer to grooming in winter.
Tanker trucks transporting thousands of liters of diesel to the site must also traverse the glacier, but their trips are not nearly as frequent since Brucejack became the first brownfield operation to convert its entire haulage fleet to battery-electric.
Mike Gagnon is Principal of Business Improvement at Newcrest. He served as Brucejack’s superintendent from November 2020 to June 2022 and has been intimately involved throughout an electrification journey that began with a tradeoff study and a single-truck trial to establish a business case, and has since resulted in underground mining’s first full haulage fleet BEV conversion.
Beyond the expected productivity advantages of faster cycle times and lower unit costs, and environmental improvements including reduced heat, noise and greenhouse gas emissions, Gagnon says de-risking a substantial amount of diesel hauling is an undervalued benefit of the transition.
Our first priority was to improve the air, the atmosphere underground for our mining team,” Gagnon said. “However, we also realized an additional important benefit. By replacing our diesel trucks underground at the Brucejack mine, we were able to save the hauling of almost 5,000 liters of diesel fuel per day up over the glacier, which is a significant safety improvement for us.
Mike Gagnon, Principal of Business Improvement at Newcrest, has been intimately involved throughout the mine’s electrification journey.

Brucejack Mine
Brucejack is located in north-western British Columbia’s Golden Triangle, approximately 950 kilometers north of Vancouver and 140 kilometers south of Newcrest’s majority-owned and operated Red Chris mine. One of the world’s highest-grade gold operations, Brucejack reached commercial production in July 2017 under Pretium Resources. Newcrest acquired Pretium and the Brucejack operation in March 2022.
Brucejack began a four-month trial of a Sandvik Z50 in October 2020. Ahsan Chaudhary, who took over as superintendent when Gagnon assumed his business improvement role, says the mine established a range of productivity KPIs, including payload, speed, cycle times and availability, to assess performance against the existing diesel fleet.
”Even though the environmental benefits are fairly well-known with the reduction of heat and noise and removing diesel from the equation, we wanted to be sure that the business case was solid for proceeding with the Z50 truck fleet,” Chaudhary says.
Over the four-month trial period, Brucejack saw a 22 percent reduction in cycle time for the average haul cycle.
”In each of the key KPI areas that we were looking at, we saw noticeable improvements compared to the existing diesel fleet,” Chaudhary says.
Having confirmed the truck’s production benefits, and with partial funding from the CleanBC Industry Fund, Brucejack embarked on a full fleet replacement. The mine invested in eight Sandvik Z50 50-metric-ton BEVs to replace its 12 30-metric-ton diesel haul trucks.
The predecessor of Sandvik TH550B, Sandvik Z50 has one of the smallest envelopes in the 50-metric-ton capacity truck class and generates twice the peak horsepower and 1/8th the heat of diesel equivalents.
With operators needing to take turns on the trial truck and getting only limited experience with the BEV technology until Brucejack commissioned the second unit in February 2022, some initially resisted the shift from conventional haulage. General Manager Sean Masse says buy-in accelerated quickly as more trucks arrived on site.

As we started to have a bigger fleet, then more and more employees were like, ‘oh yeah, this thing is way faster, it’s way quieter. I feel a lot more comfortable at the end of the day,’” Masse says. “And it also has a really good ESG aspect to it. We are reducing thousands of metric tons of carbon from our operation.
Brucejack has now removed more than 3,200 diesel horsepower from underground through a battery-electric migration that Newcrest expects will eliminate around 65,000 metric tons of CO2 emissions by the end of the decade – the equivalent emissions of 14,000 gasoline-powered passenger vehicles driven for one year. Brucejack is grid-connected, enabling the use of renewable power despite the mine’s remoteness. It predominantly operates on low-cost, low-carbon hydroelectric power, broadening the benefits of BEVs even further.

Newcrest
Newcrest is Australia’s largest gold producer and one of the world’s leading gold miners. The company operates gold and copper mines in Australia, Canada and Papua New Guinea. Newcrest produced 1.96 million ounces of gold and 121,000 metric tons of copper in FY 2022.
Brucejack commissioned its eighth and final Sandvik Z50 in March 2023. The trial truck has amassed more than 6,000 operating hours since October 2020 while the second unit recently reached 4,000. Average fleet availability has hovered around 92 percent, and Brucejack consistently achieves loaded up-ramp speeds of 14 kilometers per hour with the BEVs – 40-55 percent faster than the replaced diesel fleet.
“We’re seeing added value across the board when it comes to our production, the speed of those trucks, the cycle times on them,” says Reid Simpson, Mine Engineer, Projects, who worked on the initial tradeoff study before the trial.
You’re providing your workers a cleaner environment to work in and a more productive environment, so why not, right? It’s a no-brainer for us.

Operator Andrena Moore started at Brucejack in 2015 working snow removal before moving to surface operations a few years later and transitioning underground in 2021. She has more than 1,100 hours operating Sandvik Z50s.
“The emissions and heat difference is significant compared to the diesel trucks,” she says.
I enjoy the quiet in the cab, for sure, way, way more. Although I do use earplugs still, I’m less tired, less fatigued by the end of the day because that background sound is gone. For such a large machine, they’re quite precise. They articulate very smoothly. They can get in and out of tight spaces. They just move smoother, more gracefully.

Each day, the eight-truck fleet hauls a target of 4,000 to 5,000 metric tons of ore from underground in addition to approximately 2,500 metric tons of development waste. During a typical shift, each Sandvik Z50 is responsible for 10-15 loads and covers a total travel distance of 30-40 kilometers. The trucks swap batteries two or three times per shift, with each swap requiring manual battery disconnection and reconnection and taking as little as seven minutes, depending on charge bay efficiency. The same swap can be completed in as little as three minutes on successor Sandvik TH550B, which features Sandvik’s next-generation AutoConnect feature.
Brucejack adapted existing infrastructure for its first charge bay for the trial truck. As the mine has grown its fleet and progressed on its electrification journey, its charge bays have become more purpose-built with increasingly refined and optimized designs. Early setups include chargers on pads of crushed material followed by poured concrete pads that provide better footing for operators doing swaps.
"After that we created an elevated platform for the charging equipment that made the segregation between the mobile equipment and the fixed infrastructure more robust and gave our operators a larger working area to complete swaps", Chaudhary says.

The latest iteration utilizes the same bench concept to remove the electrical equipment from the roadway, but with the addition of a drive-through system.
“Operators no longer have to drive in and back out,” Chaudhary says. “You drive in, drop your battery and then you continue driving forward to pick up the second battery and then to leave the charge bay, you continue to drive straight through and back to the ramp.”
Sandvik supports the fleet of eight trucks and 21 battery cages under a Battery as a Service by Sandvik contract, a turnkey solution for Brucejack under which Sandvik takes full responsibility for battery maintenance, renewal and disposal. Sandvik provides a fleet manager and four onsite technicians to support the batteries and BEVs. The haulage transition success has delivered so much value that the mine commissioned a Sandvik LH518B battery-electric loader for a six-month trial in March 2023.
"I think everyone’s going to want to say they had swapped over sooner"
“Other mines have trialed the BEV loaders and we want to understand the same learnings and mimic the same benefits to understand if there’s a business case for Brucejack by implementing a battery-electric fleet for our loaders as well,” Chaudhary says.
Mine Planning Engineer Evan Robson, who alongside Simpson spearheaded the initial tradeoff study, is excited about the potential more battery-electrification has to improve productivity and working conditions at Brucejack.
”There’s a capital cost that comes with making the switch, but looking three to five years down the road, I think everyone’s going to want to say they had swapped over sooner,” Robson says. ”And I think the time’s now to do so.”


Gagnon agrees.
”For companies that are interested in battery-electric technology, I highly recommend that they reach out to Sandvik and start the discussion now, to get in line and start their own battery-electric journey,” he says. ”Sandvik for us has been a great partner to work with and helped us along the design, implementation and execution of the battery-electric project at the Brucejack mine.”
Photo: Adam Lach
Published: 22 May 2023